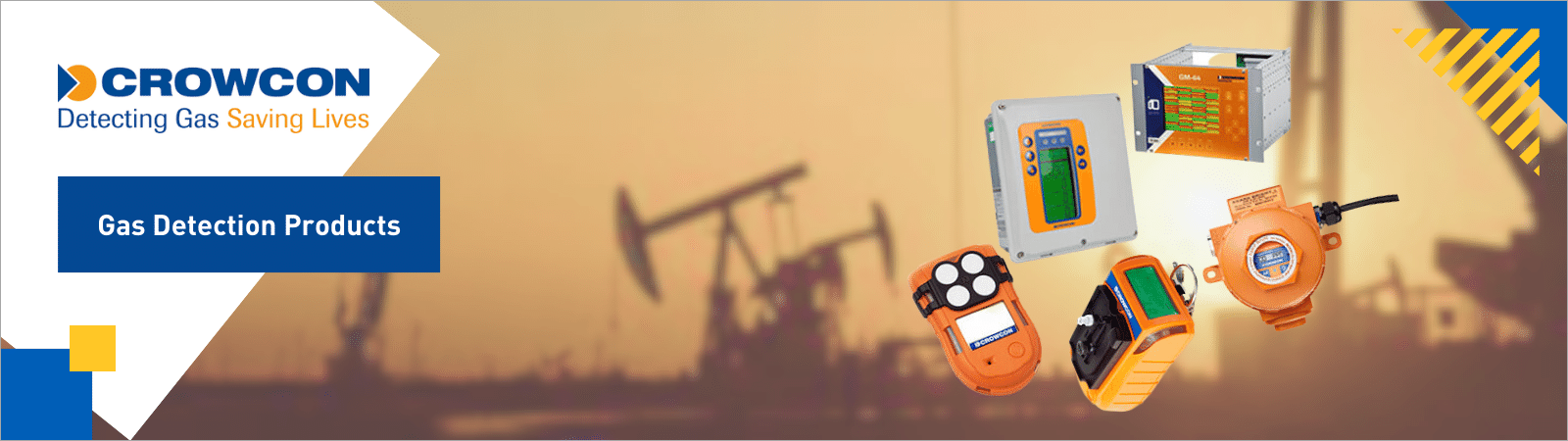
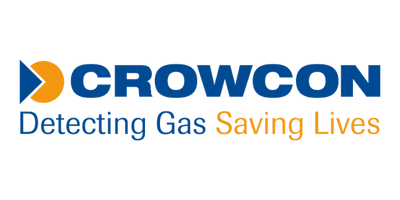
Crowcon Detection Instruments Ltd is part of the Halma family, a group of organisations dedicated to providing safety, health and environmental technologies to support organisations across multiple industries. Crowcon focus on gas detection by understanding current and future market requirements and responding accordingly. Their track record of growth speaks for itself.
Crowcon At A Glance
- Established in 1970, with continuous growth ever since
- Today, over 500,000 portable and fixed Crowcon devices are in use around world
- Leading experts in Process and Infrastructure Safety
- Pioneered over 10 technology and industry firsts
- Best in class manufacturing
- Quality focused
- Regional and industry specific certifications
Highlight
Product Categories
Portable Gas Detectors
Crowcon protects against a wide range of industrial gas hazards with its single gas and multi-gas monitors for personal monitoring and portable safety applications. With a wide range of sizes and complexities, you can select the right solution depending on the number and type of gas sensors you need and your display and certification requirements.
Fixed Gas Detectors
Crowcon offers a flexible range of products which are able to measure flammable, toxic and oxygen gases, report their presence and activate alarms or associated equipment. We use a variety of measurement, protection and communications technologies and our fixed detectors have been proven in many arduous environments, including oil and gas exploration, water treatment, chemical plants and steel mills.
They are used in many other applications where reliability, dependability and lack of false alarms are valued. These include within the automotive and aerospace manufacturing sectors, on scientific and research facilities and in high-utilisation medical, civil or commercial plants.
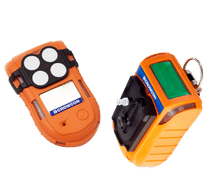
Portable Gas Detectors
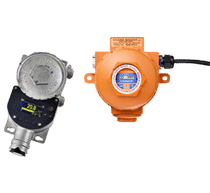
Fixed Gas Detectors
Combined with a variety of detector types, our control panels offer a flexible range of solutions which are able to measure flammable, toxic and oxygen gases, report their presence and activate alarms or associated equipment.
Crowcon fixed gas monitoring systems are designed to be interfaced with manual call points, fire and gas detectors and distributed control systems (DCS). In addition each system can be engineered to drive remote annunciators and mimic panels.
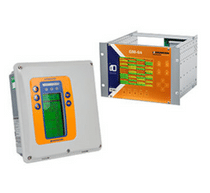
Control Panels